Precision or Speed? Comparing Pulsed and Continuous Laser Cleaning Machines
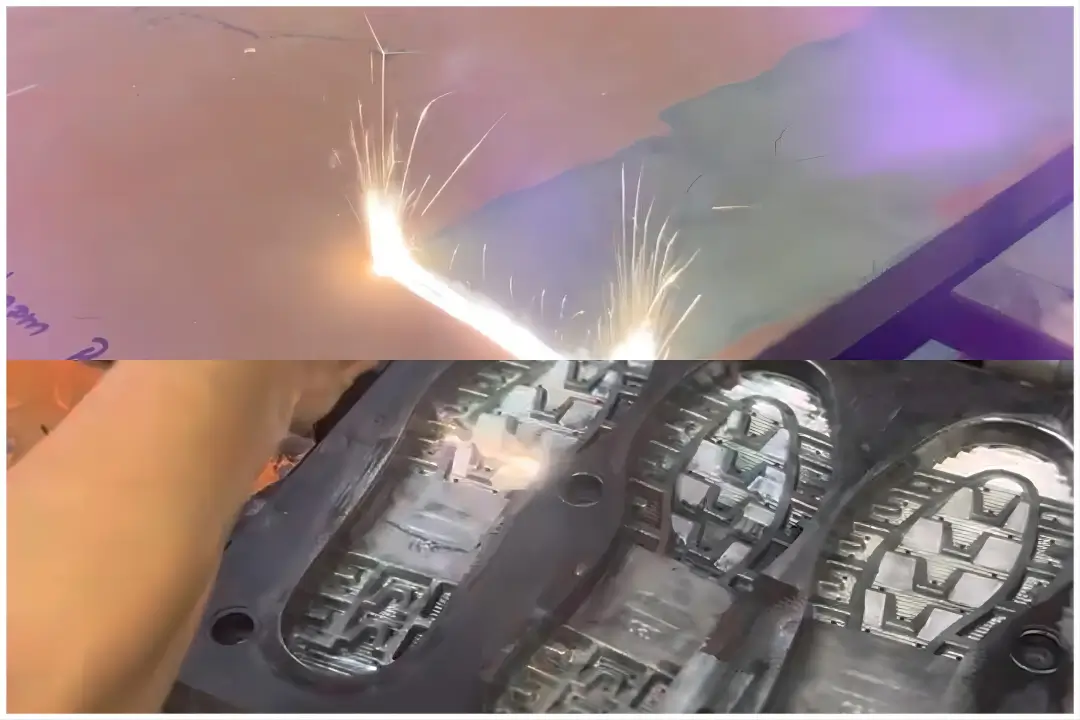
Introduction:
Laser cleaning technology has rapidly evolved, offering industries a powerful and efficient method for removing contaminants from various surfaces. Among the available options, pulsed and continuous laser cleaning machines stand out as the two primary types, each designed to meet specific cleaning needs and application scenarios. Understanding the differences between these two technologies is crucial for making the right choice depending on the task at hand.
In this comprehensive guide, we will delve into the distinctions between pulsed and continuous laser cleaning machines, exploring their working principles, advantages, disadvantages, and ideal application scenarios.
Understanding Laser Cleaning Technology
Laser cleaning involves using a focused laser beam to remove contaminants, rust, paint, or other unwanted substances from a surface. The process works by directing the laser energy onto the surface, where it interacts with the material to break down and vaporize the contaminants without damaging the underlying substrate.
Laser cleaning has become increasingly popular due to its non-abrasive nature, environmental friendliness, and precision. It is used in various industries, including aerospace, automotive, manufacturing, and electronics, where cleanliness and surface quality are of paramount importance.
The two main types of laser cleaning machines are pulsed and continuous, each with distinct characteristics that make them suitable for different tasks.
Pulsed Laser Cleaning Machines: Precision and Control
Pulsed laser cleaning machines are designed to deliver laser energy in short, high-intensity bursts or pulses. The common laser power is 200W or 100W, there is 300W or 500W for option as well. This pulsed delivery allows for precise control over the laser energy applied to the surface, making it ideal for cleaning tasks that require accuracy and minimal impact on surrounding materials.
Working Principle
Pulsed laser cleaning machines emit short, high-energy pulses of laser light. Each pulse lasts for a very brief period, typically in the range of nanoseconds to microseconds. The high peak power of each pulse creates an intense, localized interaction with the surface contaminants, causing them to vaporize or ablate without significantly heating or damaging the substrate.
The short duration of the pulses ensures that the heat-affected zone (HAZ) is minimal, making this technology suitable for cleaning delicate or heat-sensitive materials.
Advantages of Pulsed Laser Cleaning Machines
- High Precision: The pulsed nature of the laser allows for precise control over the energy delivered to the surface. This precision is crucial when dealing with intricate surfaces, fine parts, or materials that are sensitive to heat.
- Minimal Heat-Affected Zone: The short pulse duration minimizes the amount of heat transferred to the substrate, reducing the risk of thermal damage or deformation. This makes pulsed laser cleaning ideal for applications where maintaining the integrity of the substrate is critical.
- Effective on Complex Surfaces: Pulsed laser cleaning is particularly effective on complex or uneven surfaces. The ability to focus the laser energy on specific areas allows for targeted cleaning without affecting the surrounding material.Under same laser power, the cleaning of paints by pulsed laser is 3 to 7 times faster than continuous laser with better finish.
- Versatility: Pulsed laser cleaning machines can be used on a wide range of materials, including metals, plastics, ceramics, and composites. They are also effective in removing a variety of contaminants, such as oxide layers, coatings, welding slag, and rust.
Disadvantages of Pulsed Laser Cleaning Machines
- Slower Cleaning Speed: Due to the focus on precision, pulsed laser cleaning is generally slower than continuous laser cleaning, especially when dealing with large surface areas.
- Higher Cost: Pulsed laser systems tend to be more expensive to manufacture and maintain due to their complex design and the need for precise control mechanisms.
- Requires Skilled Operation: The precision and control offered by pulsed laser cleaning machines require operators with a higher level of expertise to ensure optimal results and avoid damage to sensitive materials.
Ideal Application Scenarios for Pulsed Laser Cleaning
- Fine Parts Cleaning: Pulsed laser cleaning is ideal for tasks that require the removal of contaminants from small, intricate components, such as those found in electronics or aerospace applications.
- Oxide Layer Removal: The precision of pulsed lasers makes them perfect for removing thin oxide layers from metal surfaces without damaging the underlying material.
- Welding Slag Removal: Pulsed laser cleaning can effectively remove welding slag and other residues from welds, ensuring a clean and smooth surface.
- Heat-Sensitive Materials: When working with materials that are prone to heat damage, such as thin metals or certain plastics, pulsed laser cleaning offers a safe and effective solution.
Continuous Laser Cleaning Machines: Efficiency and Speed
Continuous laser cleaning machines, as the name suggests, emit a continuous beam of laser light, providing a stable and consistent energy output. The laser power can be 1000W, 1500W or 2000W for handheld type, 3000W, 4000W or 6000W for robotic arm integration. This makes them well-suited for tasks that require rapid cleaning of large, flat surfaces.
Working Principle
Continuous laser cleaning machines deliver a steady stream of laser energy, which is absorbed by the surface contaminants. The energy causes the contaminants to heat up, melt, or vaporize, effectively cleaning the surface. The continuous nature of the laser beam allows for high-speed cleaning, making this technology ideal for large-scale applications.
Advantages of Continuous Laser Cleaning Machines
- High Cleaning Speed: Continuous laser cleaning machines are capable of processing large surface areas quickly, making them ideal for high-throughput applications.
- Cost-Effective: Generally, continuous laser systems are less expensive to produce and maintain compared to pulsed systems, making them a cost-effective choice for large-scale industrial cleaning.
- Stable and Consistent Performance: The continuous energy output provides a stable and consistent cleaning process, ensuring uniform results across the entire surface.
- Easy Integration: Continuous laser cleaning machines are often easier to integrate into automated production lines, making them suitable for industries that require high levels of automation.
Disadvantages of Continuous Laser Cleaning Machines
- Larger Heat-Affected Zone: The continuous nature of the laser beam results in a larger HAZ, which can cause thermal damage or deformation to heat-sensitive materials.Removal of paints by continuous laser may lead to serious remelting phenomenon and laser texture.
- Less Precision: Continuous laser cleaning is less precise than pulsed laser cleaning, making it less suitable for tasks that require fine control or detailed work.
- Limited Effectiveness on Complex Surfaces: Continuous laser beams may struggle to clean intricate or uneven surfaces effectively, as the energy is spread over a larger area and may not reach all parts of a complex surface.
Ideal Application Scenarios for Continuous Laser Cleaning
- Large Surface Area Cleaning: Continuous laser cleaning is ideal for tasks that involve cleaning large, flat surfaces, such as removing paint, grease, or dust from metal sheets or pipelines.
- Industrial Cleaning: Industries that require rapid and efficient cleaning of large areas, such as automotive manufacturing or shipbuilding, can benefit from the high-speed capabilities of continuous laser cleaning machines.
- Surface Preparation: Continuous laser cleaning is effective for preparing surfaces for further processing, such as painting or coating, by removing contaminants quickly and efficiently.
- Less Heat-Sensitive Materials: When working with materials that can withstand higher levels of heat, continuous laser cleaning provides a fast and effective solution.
Comparing Pulsed and Continuous Laser Cleaning Machines
The key differences between pulsed and continuous laser cleaning machines lie in their laser output modes, cleaning effects, and suitable application scenarios. Here’s a comparison of the two technologies:
Feature |
Pulsed Laser Cleaning |
Continuous Laser Cleaning |
Laser Output Mode |
Pulses with high peak power |
Continuous wave with stable power |
Cleaning Speed |
Slower, focused on precision |
Faster, suitable for large areas |
Precision |
High, suitable for intricate surfaces |
Moderate, suitable for flat surfaces |
Heat-Affected Zone |
Minimal, reduces thermal damage |
Larger, higher risk of thermal damage |
Cost |
Higher, due to complex design |
Lower, more cost-effective for large-scale tasks |
Ideal Applications |
Fine parts, heat-sensitive materials, complex surfaces |
Large surface areas, industrial cleaning, surface preparation |
Effectiveness on Complex Surfaces |
Highly effective, can target specific areas |
Less effective, may struggle with uneven surfaces |
Choosing the Right Laser Cleaning Machine for Your Needs
Selecting the right laser cleaning machine depends on the specific requirements of your application. Here are some factors to consider:
- Surface Complexity: If your cleaning task involves complex or intricate surfaces, a pulsed laser cleaning machine is likely the better choice due to its precision and control.
- Material Sensitivity: For materials that are sensitive to heat, such as thin metals or certain plastics, pulsed laser cleaning offers a safer option with minimal risk of thermal damage.
- Cleaning Speed: If you need to clean large areas quickly, and the material can withstand some level of heat, a continuous laser cleaning machine will provide the speed and efficiency required.
- Budget: Continuous laser cleaning machines are generally more cost-effective, making them a good choice for large-scale industrial applications where cost is a significant factor.
- Required Surface Quality: If the task requires high surface quality with minimal impact on the substrate, pulsed laser cleaning will deliver the best results.
- Industry Requirements: Consider the specific demands of your industry. For example, the aerospace and electronics industries often require the precision of pulsed laser cleaning, while automotive and shipbuilding may benefit from the efficiency of continuous laser cleaning.
Conclusion
Both pulsed and continuous laser cleaning machines offer unique advantages and are suitable for different application scenarios. Pulsed laser cleaning excels in precision, making it ideal for tasks that require fine control and minimal heat impact. Continuous laser cleaning, on the other hand, provides efficiency and speed, making it the preferred choice for large-scale industrial cleaning tasks.
By understanding the differences between these two technologies, you can make an informed decision that best suits your application.