How to Weld Aluminum and Copper: A Comprehensive Guide
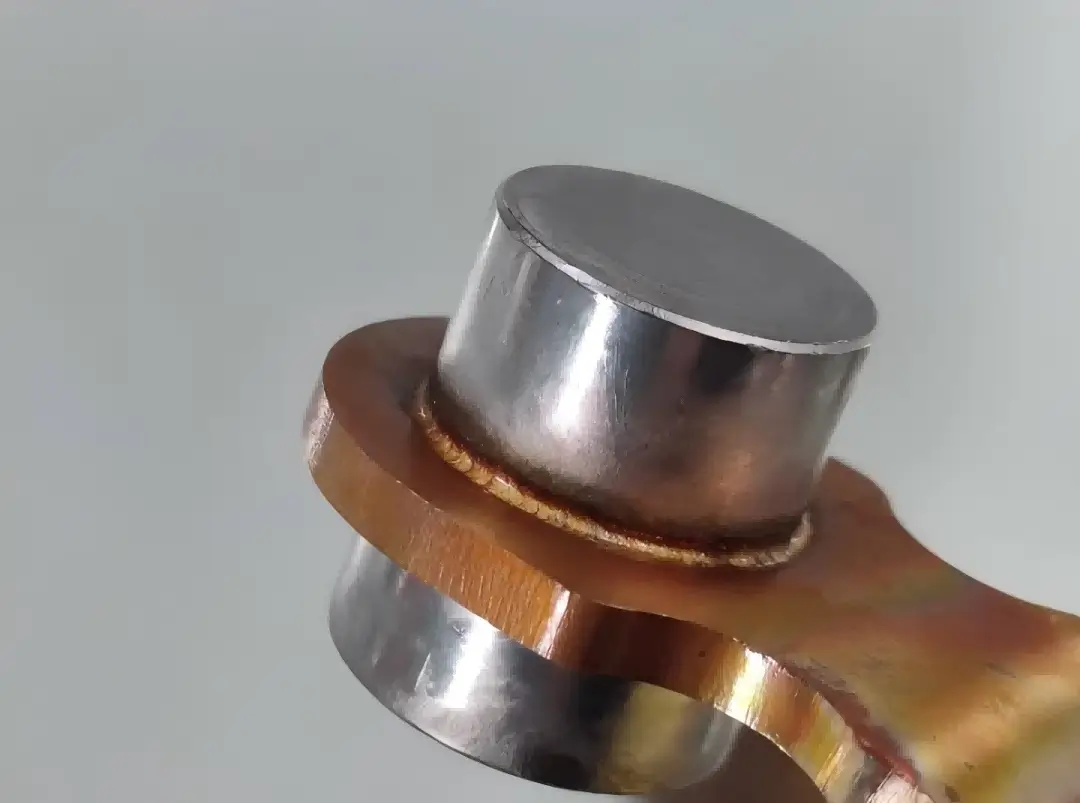
Introduction
Welding aluminum and copper is a process fraught with challenges, yet it holds immense potential in various industries where combining these two metals can yield significant benefits. These metals are often selected for their unique properties—aluminum is lightweight and corrosion-resistant, while copper is known for its exceptional electrical conductivity and thermal properties. However, their dissimilar characteristics also present difficulties that require specialized techniques and thorough preparation to achieve a successful weld. This comprehensive guide explores the complexities of aluminum-copper welding, detailing various welding techniques, their advantages, limitations, and the critical considerations to ensure strong, durable bonds.
Understanding the Challenges
Welding dissimilar metals like aluminum and copper involves a number of challenges, primarily due to their differing physical and chemical properties. Here are the key challenges to understand before attempting to weld these metals:
1. Melting Point Disparity
One of the most significant challenges in welding aluminum and copper is the disparity in their melting points. Aluminum melts at around 660°C (1220°F), whereas copper has a much higher melting point of approximately 1085°C (1984°F). This considerable difference makes it difficult to create a stable weld pool that fuses both metals adequately. If not carefully controlled, this can lead to incomplete fusion or excessive melting of aluminum, leading to weak joints.
2. Thermal Conductivity
Both aluminum and copper are excellent conductors of heat, but this very property complicates the welding process. Their high thermal conductivity means that heat dissipates rapidly from the weld area, making it challenging to maintain a consistent temperature at the joint. This can result in an insufficient heat concentration, leading to poor fusion between the metals and potential defects in the weld.
3. Oxidation
Aluminum is highly reactive with oxygen and readily forms a tough oxide layer (Al2O3) on its surface when exposed to air. This oxide layer is more challenging to melt than the base aluminum metal and can act as a barrier to the welding process, preventing proper metal-to-metal contact. Copper, on the other hand, forms oxides at a slower rate, but these oxides can still interfere with the quality of the weld if not properly managed.
4. Galvanic Corrosion
When aluminum and copper are joined together in the presence of an electrolyte (e.g., water), there is a risk of galvanic corrosion. This electrochemical process occurs because aluminum is more anodic than copper, meaning it is more likely to corrode when in contact with copper. To prevent this, protective coatings or barriers may be needed, or alternative joining methods should be considered.
Pre-Welding Preparation
Preparation is key to overcoming the challenges associated with welding aluminum and copper. The following steps should be meticulously followed to ensure the best possible outcomes:
1. Cleaning
Before welding, both aluminum and copper surfaces must be thoroughly cleaned to remove contaminants such as oils, greases, dirt, and oxides. Mechanical cleaning methods, such as wire brushing or grinding, are effective in removing surface oxides. For aluminum, a stainless steel wire brush is often used to avoid embedding other materials that could cause contamination. Chemical cleaning with solvents or etching solutions may also be used to ensure the surfaces are free from impurities that could affect the weld.
2. Joint Design
The design of the joint plays a crucial role in the success of the weld. Depending on the specific application and the mechanical properties required, different joint geometries can be employed. For instance, lap joints may be preferred for their simplicity, but they might not provide the strength needed for high-stress applications. Butt joints, on the other hand, can offer better load distribution but require precise alignment and preparation. Consideration must also be given to the thickness of the materials, as this will influence the heat input and the welding technique to be used.
3. Filler Metal Selection
Selecting the appropriate filler metal is critical when welding aluminum and copper. The filler metal must be compatible with both base metals and possess the necessary mechanical properties to achieve a strong, durable joint. Commonly used filler metals include aluminum-silicon alloys (e.g., 4047 or 4043) and copper-silver alloys, which help bridge the gap between the two metals’ properties. The choice of filler metal will also depend on the specific welding process used and the intended application of the welded component.
Welding Techniques
Several welding techniques can be employed to join aluminum and copper, each with its own set of advantages and limitations. Below, we explore the most common methods and their suitability for different applications:
1. Laser Welding
Laser welding is a precise and controlled welding method that uses a focused laser beam to melt and fuse the metals at the joint. This technique is particularly well-suited for welding dissimilar metals like aluminum and copper due to its high precision and ability to localize heat input, minimizing the heat-affected zone (HAZ).
Advantages: Laser welding offers excellent control over the welding process, producing high-quality, strong welds with minimal distortion. The localized heat input reduces the risk of thermal damage to surrounding areas, making it ideal for applications where precision is critical. Additionally, laser welding can be automated, making it suitable for high-volume production.
Weld smaller shapes on smaller diameters, parts with diameters less than 1 mm but greater than 200 grams can be welded.
No preheating required, no heat input during welding, stable weld pool.
Disadvantages: The main drawbacks of laser welding are its high cost and complexity. The equipment required for laser welding is expensive, and the process often demands skilled operators or advanced automation systems. Additionally, laser welding may be limited in terms of material thickness, with thicker sections requiring multiple passes or preheating to achieve full penetration.
Applications: Laser welding is commonly used in industries where precision and strength are paramount, such as aerospace, electronics, and automotive components. It is particularly useful for welding thin sheets or small components where other welding methods may struggle to maintain control.
2. TIG (Tungsten Inert Gas) Welding
TIG welding, also known as Gas Tungsten Arc Welding (GTAW), is a versatile welding process that uses a non-consumable tungsten electrode to create an arc in a shielding gas, typically argon or helium. The process is known for producing clean, high-quality welds with excellent control over the heat input.
Advantages: TIG welding is highly versatile and can be used to weld a wide range of metals, including aluminum and copper. The process offers precise control over the welding parameters, allowing for the creation of high-quality welds with minimal spatter and distortion. TIG welding also allows for the use of filler metal, which can be selected to match the properties of the base metals.
Disadvantages: TIG welding is a skill-intensive process that requires a high level of expertise to perform correctly. It is also slower compared to other welding methods, which can increase labor costs. Additionally, the equipment used for TIG welding is generally more expensive, and the process requires a high degree of cleanliness to avoid contamination of the weld.
Applications: TIG welding is widely used in industries where high-quality welds are essential, such as aerospace, marine, and general fabrication. It is particularly well-suited for welding aluminum and copper in applications where precision and control are required.
3. Stick Welding (SMAW)
Shielded Metal Arc Welding (SMAW), commonly known as stick welding, is a manual welding process that uses a consumable electrode coated with flux to create an arc. The process is known for its versatility and accessibility, making it one of the most widely used welding methods.
Advantages: Stick welding is relatively easy to learn and can be performed with minimal equipment, making it accessible for a wide range of applications. The process is versatile and can be used in various positions and environments, including outdoor settings. Stick welding is also effective at welding thicker materials, which can be challenging for other welding methods.
Disadvantages: Stick welding is less precise than other welding methods, and the resulting welds may require more cleanup due to slag formation. The process also generates more spatter, which can affect the appearance of the weld and increase post-weld cleanup time. Additionally, stick welding may not provide the level of control needed for welding dissimilar metals like aluminum and copper.
Applications: Stick welding is commonly used in general construction, maintenance, and repair work. While it is not the first choice for welding aluminum and copper, it can be used in situations where precision and appearance are less critical, and the emphasis is on practicality and ease of use.
4. Friction Welding
Friction welding is a solid-state welding process that generates heat through mechanical friction between the workpieces, followed by forging them together to create a bond. This technique is particularly effective for joining dissimilar metals, as it does not involve melting, reducing the issues associated with differing melting points.
Advantages: Friction welding produces strong joints with excellent mechanical properties, as the process avoids the issues associated with melting and solidification. The absence of a molten pool reduces the risk of defects such as porosity or cracking. Friction welding is also highly efficient, with short cycle times and minimal material wastage.
Disadvantages: The main limitation of friction welding is the need for specialized equipment, which can be costly and complex to set up. The process is also limited to certain joint geometries, such as cylindrical shapes, and may not be suitable for all applications. Additionally, the initial setup and alignment of the workpieces are critical to the success of the weld.
Applications: Friction welding is widely used in the automotive, aerospace, and industrial machinery sectors. It is particularly useful for joining aluminum and copper in applications where high strength and durability are required, such as in electrical connectors and automotive components.
5. High-Frequency Welding
High-frequency welding is a process that uses electromagnetic fields to induce heat in the metals, causing them to melt and fuse together. This technique is often used for welding thin sheets or tubular structures, where speed and precision are critical.
Advantages: High-frequency welding offers several advantages, including high-speed operation, strong welds, and minimal heat-affected zones. The process is highly efficient, making it suitable for mass production of components such as tubing, pipes, and wires. The precise control over the welding parameters also allows for consistent, high-quality welds.
Disadvantages: The primary disadvantages of high-frequency welding are the high cost of the equipment and the complexity of the process. The technique requires specialized machinery and skilled operators, which can increase the overall cost of production. Additionally, the process may be limited in terms of material compatibility and joint design, making it less versatile than other welding methods.
Applications: High-frequency welding is commonly used in the production of tubing, pipes, and wires, where the combination of speed and precision is essential. It is also used in the automotive and electronics industries for welding aluminum and copper in components such as heat exchangers and electrical connectors.
6. Brazing
Brazing is a joining process that uses a filler metal with a lower melting point than the base metals. The filler metal is heated and flows into the joint by capillary action, creating a bond between the workpieces without melting them.
Advantages: Brazing offers several advantages, including the ability to join dissimilar metals, lower temperature requirements, and minimal thermal distortion. The process is also relatively simple and can be performed with standard equipment, making it accessible for a wide range of applications. Brazing also allows for the creation of complex joints with good mechanical properties.
Disadvantages: The main drawback of brazing is that the resulting joints are generally weaker than those produced by welding. The process also requires careful control of the heating to avoid overheating or damaging the base metals. Additionally, brazing may not be suitable for high-stress applications where maximum strength is required.
Applications: Brazing is commonly used in the production of heat exchangers, plumbing fittings, and other components where the ability to join dissimilar metals is advantageous. It is also used in the electronics industry for joining copper and aluminum in applications where the operating temperature is relatively low, and the mechanical load is moderate.
Post-Welding Considerations
After completing the welding process, several post-weld operations may be necessary to ensure the quality and longevity of the weld:
1. Inspection
A thorough visual inspection of the weld is essential to identify any surface defects, such as cracks, porosity, or incomplete fusion. For critical applications, non-destructive testing methods, such as ultrasonic testing or radiography, may be employed to detect subsurface defects that are not visible to the naked eye.
2. Testing
Mechanical testing, such as tensile, bend, or hardness tests, can be performed to verify the strength and quality of the weld. These tests provide valuable information about the weld’s mechanical properties and its ability to withstand operational stresses.
3. Heat Treatment
In some cases, post-weld heat treatment may be necessary to relieve residual stresses and improve the weld’s mechanical properties. This is particularly important for applications where the welded component will be subjected to high-stress or thermal cycling.
Choosing the Right Technique
Selecting the optimal welding method for aluminum and copper depends on several factors, including:
- Joint Design: The geometry of the joint and the required strength will influence the choice of welding method.
- Material Thickness: Thicker materials may require welding techniques that provide deeper penetration, such as laser welding or friction welding.
- Required Strength and Durability: For high-stress applications, methods that produce stronger joints, such as friction welding, may be preferred.
- Production Volume: High-volume production may benefit from automated processes like laser welding or high-frequency welding.
- Operator Skill Level: Some welding methods, such as TIG welding, require a high level of skill, which may influence the choice based on available expertise.
- Equipment Availability: The availability and cost of welding equipment can also be a deciding factor.
Additional Tips
To ensure successful welding of aluminum and copper, consider the following best practices:
- Cleanliness: Keep the welding area and materials clean to prevent contamination and defects in the weld.
- Proper Joint Fit: Ensure a tight fit between the parts to minimize gaps and achieve proper penetration.
- Filler Metal Selection: Choose a filler metal that matches the mechanical properties of the base metals and is compatible with the welding process.
- Shielding Gas: Use a shielding gas that is appropriate for the welding method and provides adequate protection from atmospheric contaminants.
- Operator Skill: Ensure that the operator has the necessary skills and experience for the chosen welding method.
Conclusion
Welding aluminum and copper is a complex process that requires a deep understanding of the materials’ properties and the challenges involved. By carefully selecting the appropriate welding technique and following best practices, it is possible to create strong, reliable joints that meet the specific requirements of the application. Whether you’re working in aerospace, automotive, electronics, or any other industry, mastering the art of aluminum-copper welding can open up new possibilities for innovation and design.