Best Way to Remove Slags on Laser Cutter Table
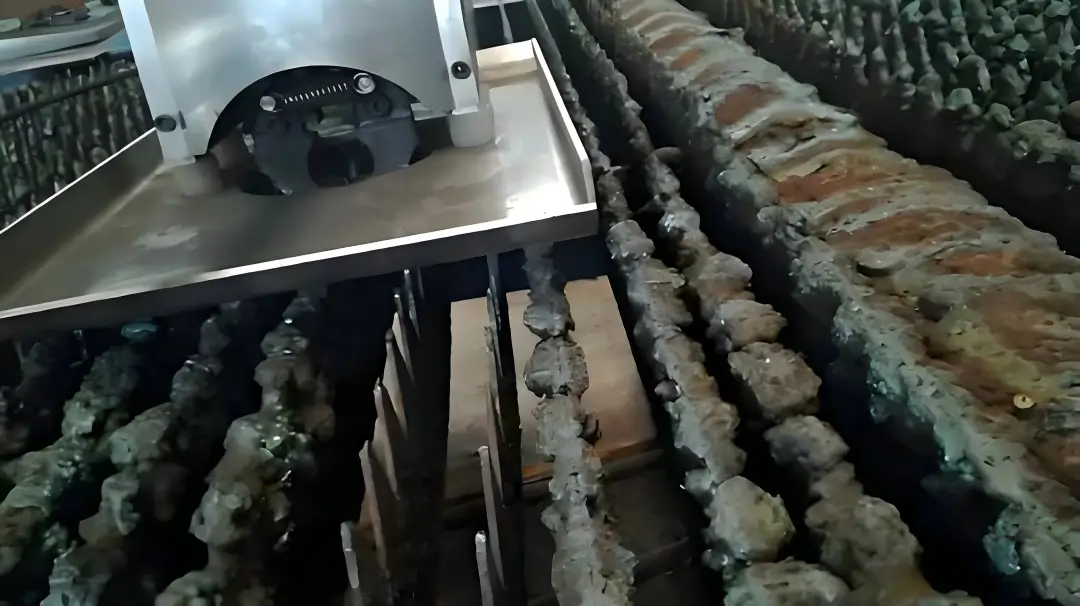
(8 Different Ways with Pos and Cons)
Over time, slag can build up on the slats of a fiber laser cutting machine, which can affect the cutting quality and even result in material waste. Cleaning these slags is essential but can often be a frustrating task. Below are 8 methods for removing or reducing slag buildup to help maintain optimal cutting performance.
1. Hammer or Crowbar
Pros:
- Easy to use and inexpensive, often free.
Cons:
- Very slow and labor-intensive.
This method is best for occasional or light use, especially when dealing with minimal slag or in situations with flexible production schedules. However, it is not practical for mass production.
2. Homemade Slag Remover
Pros:
- Low cost, requires less physical effort than using a hammer.
Cons:
- Low efficiency and requires some design and fabrication skills.
This option is ideal for removing slight slag, offering an affordable yet basic solution.
3. Impact Drill
Pros:
- Affordable and easy to find, with better efficiency than manual methods.
Cons:
- Noisy and may not remove all slag thoroughly.
An impact drill is a more efficient solution for moderate cleaning, but it may not provide a deep clean for stubborn slag.
4. Electric Slag Remover
Pros:
- Highly efficient and reduces physical labor by vibrating to remove slag.
Cons:
- Struggles with severe slag, especially on high-power lasers (10KW+). Can be noisy, cause hand numbness, and requires maintenance. Cost: around $700 per set.
This is a good solution for regular cleaning, though it may not be sufficient for heavy slag buildup.
5. Copper Saw-Slat
Pros:
- Copper slats obviously reduce slag buildup due to their high boiling point (2360℃) and good thermal conductivity. Usually copper grates last for 6 times longer time than steel ones.
Cons:
- Copper slats are expensive (over thousand USD cost) and can’t completely prevent slag. Using a fiber laser to cut copper slats poses a risk to the machine’s cutting head and laser generator. Not all laser generator can work well with copper slat, due to its high reflection rate to laser light.
While effective in reducing slag, this option requires a significant initial investment.
6. Slat Shield Agent
Pros:
- Spraying slat shield agent helps reduce slag, and any slight slag buildup is easy to remove. Requires minimal physical effort and is easy to apply.
Cons:
- Costs around $10/m² and needs to be reapplied periodically. The product must comply with safety regulations like MSDS.
This method is excellent for preventing heavy slag buildup and makes future cleaning easier.
7. Slat Deburring Machine
Pros:
- Extremely efficient and effortless; thoroughly removes slag. It can also be used for other metal products.
Cons:
- Expensive (around $10,000) and noisy. The abrasive belt requires periodic replacement.
This is a long-term solution for high-volume production, but the high cost may not be justified for smaller operations.
8. Replacing Slats
Pros:
- The laser machine can cut new slats easily, and selling old slats can offset the cost.
Cons:
- Time-consuming and incurs the cost of materials. Ensuring proper sizing is essential for the machine to function correctly.
This method offers a fresh start but is best used in combination with other methods to delay the need for replacements.
Conclusion
No single method offers a perfect, low-cost solution for removing slag thoroughly and quickly. A combination of approaches, such as using copper slats, slat shield agents, and an electric slag remover or manual methods, can be effective. The key is regular maintenance to prevent heavy slag buildup. For high-power lasers (10KW+), replacing slats may eventually be necessary, and selling the old slats can help mitigate costs.